Latest news &
press releases
Data sharing in dangerous goods logistics – CHEManager 02/2025
19.02.2025 – Despite complex requirements, even medium-sized companies can modernise their processes and position themselves for future growth through digitalisation and innovative approaches. This is shown by the example of Scheren Logistik, a family business that specialises in the storage of hazardous materials for the chemical and pharmaceutical industries.
In addition to 40,000 pallet spaces and daily handling of around 50 lorries, the logistics company offers a wide range of additional services – including sampling, interface management and refrigerated storage. With innovative solutions, 32-year-old Managing Director Björn Scheren wants to master the key challenges facing his company and make operations efficient and future-proof. He describes personnel as the biggest challenge, referring not only to recruitment in his company, but also and especially to the haulage companies commissioned by customers.
“Staff turnover is increasing enormously, in our warehouse and especially among lorry drivers. This is critical for us, because if drivers are dissatisfied or don’t understand processes, the entire process comes to a standstill,” explains Scheren. Waiting times are a frequent cause of frustration, which not only affects efficiency but also the satisfaction of everyone involved. And waiting times quickly arise when the variety of languages increases and makes everyday work more difficult on both sides, which is particularly true for the complex processes in chemical logistics. “The requirements for the drivers not only vary depending on the product group – for example with regard to load securing or seals – but also have to be communicated in different languages. In our despatch office, it’s pure paperwork madness,” says Scheren, describing the situation.
Every notice is translated into five languages. In addition, regulations such as the signing of CMR documents or compliance with IMO guidelines for the transport of dangerous goods by sea required a lot of explanatory work.
Even though Scheren is trying to standardise processes, it remains a challenge to meet the requirements of all customers in a uniform and efficient manner. In addition, customer requirements vary considerably. A lot of information is only available in internal work instructions and notes, as there was previously no methodology for communicating the respective requirements at the loading points clearly and in multiple languages. A clear plan was developed to change this. With the help of innovative digital solutions such as Loady, a standardised data hub developed specifically for the requirements of supply chain and chemical logistics, processes and communication with customers, freight forwarders and drivers are to be sustainably improved.
In future, drivers should be able to access structured and multilingual information that is easy to understand thanks to clear displays and visual elements. It is also expected that this will create standardised processes for customers and haulage companies. “We no longer have to define the requirements for drivers individually for each customer, but can use them across the board. With Loady, we enable our customers to use our requirements data. It takes very little effort and everything that applies to the delivery or collection of the respective products from our warehouse can be transferred directly to our customers’ communications with the haulage companies,” says Scheren. Customers and the haulage companies they commission are also informed directly of any changes. This minimises waiting times and makes the processes more pleasant for the drivers, who now have access to the information in their own language and can understand it better. For Scheren, one thing is certain: “With the right digital tools and a clear focus on the needs of our customers and partners, we can not only master the current challenges, but also remain successful in the long term.“ (bm)
Source (last update: 19.02.2025): Datenteilen in der Gefahrstofflogistik | CHEManager

Loady and Trusted Carrier announce their partnership
Digitalization and automation in logistics are only possible with reliable data that is digitally available at all times. The two platforms Loady and Trusted Carrier are pursuing precisely this goal and have concluded a cooperation agreement to simplify implementation.
- Industrial customers and transport service providers who want to optimize their logistics will benefit from the agreement between the two master data providers
- In the first joint deployment at BASF’s Ludwigshafen site, the partners cover all processes from transport preparation to fully automated truck dispatch and right through to the loading point in an end-to-end digital process
Mannheim / Frankfurt, 16 December 2024 – Loady and Trusted Carrier, two innovative platforms that provide standardized master data for digital logistics are entering into a partnership for collaboration and joint activities with industrial customers. What both solutions have in common is that they provide data that, for the first time ever, can be managed centrally, structured and, above all, at first hand and then shared with other companies via open interfaces. The focus of the two platforms is 100% complementary:
In the case of Trusted Carrier, the focus is on current information about vehicles and drivers, i.e. truck and equipment types, loading capacities or the validity of driving licenses.
Loady is about requirements and instructions for loading and unloading at various locations and loading points, i.e. opening and loading times, applicable handling processes or required technical equipment.

Fig. 1: Philipp Rennert and Lorena Meyer from Trusted Carrier and Elzbieta Wiankowska and Stefanie Kraus from Loady want to empower the automation of logistics with reliable master data
Harmonization of data and easy verification of logistics requirements
Philipp Rennert and Lorena Meyer, Chief Sales Officer and Project Manager at Trusted Carrier, and Stefanie Kraus and Elzbieta Wiankowska, CEO and COO at Loady, agree: the joint approach of their two solutions enables industrial customers to optimize truck handling at the gate and loading points. Their goal is to radically digitalize the still very manual and error-prone flow of information in the highly fragmented logistics industry. Truck journeys that are poorly planned, under-equipped or with under-qualified drivers will become less common with their two solutions – reliability and predictability in the supply chain logistics will increase.

Fig. 2: Pre-checking trucks using Loady’s target values and Trusted Carrier’s actual values is so easy
“With digitally available data from Loady and Trusted Carrier, shippers, freight forwarders and consignees are working together seamlessly for the first time. Our joint approach saves all business and logistics partners valuable time and therefore money. This is a key success factor for the further digitalization and automation of logistics. Our two platforms provide critical components for end-to-end visibility in supply chain systems and the success of current digitalization and optimization initiatives,” says Elzbieta Wiankowska, co-founder and COO of Loady GmbH. “Control along the process chain, e.g. as part of a supply chain control tower, is actually unthinkable without reliable information from Loady or Trusted Carrier,” adds Philipp Rennert. “For safety reasons alone, every industrial company should be able to know who is on their premises and whether the driver, truck and product have their paperwork in order and meet transportation requirements – all without time-consuming and error-prone manual processes.”
Trusted Carrier and Loady support automation of truck execution at BASF
The first joint customer of Loady and Trusted Carrier, BASF in Ludwigshafen, is currently in the process of automating the truck handling processes at the site. Data from both platforms, Trusted Carrier and Loady, is to be merged for check-in. The aim of Thomas Grunwald, Head of Truck Handling at BASF, is to reduce throughput times at the gate, manual effort and the number of vehicle rejections due to missing or faulty transport equipment. „With up to 2.000 trucks a day, we expect to save time thanks to automated checks. The data from Trusted Carrier provides us with actual information on the driver, vehicle and equipment used and the validity of the necessary documents. The information from Loady in turn helps us to read out the target requirements, which vary depending on the product and the loading point.”
At BASF, the inspection itself is integrated into the star/trac yard management system. The interfaces available on both platforms enable their data to be integrated into a wide range of transport logistics solutions.
About Loady GmbH
Loady is the first data hub for sharing loading requirements in supply chain logistics. The Mannheim-based startup was founded in 2023 out of the chemical industry to address a long-standing disconnect in digital collaboration and ensure smooth first and last miles in industrial transportation. With its standardized data model, API interfaces and user-specific views in 7 European languages so far, Loady enables effective digital communication of current loading and unloading requirements. Shippers, consignees, external warehouses, tank farms, freight terminals and industrial park operators who manage their data on Loady and share it with their ecosystem speed up the entire logistics process, reduce efforts, costs and CO2 emissions. Data from over 1.500 products and 45 locations in Europe is already available in Loady for the transportation industry.
Further information can be found at www.loady.com.
Press contact Loady:
Stefanie Kraus
Phone +49 151 23712351
stefanie.kraus@loady.com
About Trusted Carrier
Trusted Carrier GmbH & Co. KG was founded in 2021 on the initiative of the German Road Haulage, Logistics and Disposal Association (BGL). Trusted Carrier is the trustworthy, digital and open platform between the shipping industry, transport partners and drivers. Participating partners use the portal to exchange company, component and driver master data, which is 100% checked and validated by Trusted Carrier. Drivers are equipped with a GDPR-compliant and biometrically secured app on their smartphone or onboard unit, which meets the highest security requirements. This creates a direct communication channel into the driver’s cab for everyone involved in the process. Additional functionalities include the exchange of electronic documents, driver community offers and the integration of other partner offers in the logistics industry. Trusted Carrier started in the chemical industry in Germany and is now expanding its solution with partnerships in related sectors such as the petrochemical and pharmaceutical industries, as well as providing services in other European countries. More information at www.trusted-carrier.com
Press contact Trusted Carrier:
Philipp Rennert
Phone +49 1718654350
philipp.rennert@trusted-carrier.com
Master data – the hot potato in logistics
Since the beginning of my professional career, I have heard time and again how much companies suffer from poor master data quality in logistics and how urgently this issue needs to be addressed. In particular, the master data for loading and unloading requests is a pain for everyone involved – shippers, forwarders and consignees.
But concrete measures and tangible improvements? I see little of that. Nothing has changed in the last 20 years, especially in the area of loading and unloading requirements. Shippers, logistics providers and consignees all work in their own silos and don’t communicate with each other. How can they when no standards have been defined and communication has been the same for decades?
Collaboration is the key
Collaboration across the supply chain network is essential to achieve sustainable master data optimisation in logistics. Suppliers with their customers, shippers with their freight forwarders, warehouse service providers, industrial parks with industrial companies – everyone has to pull together. However, I see far too few of these initiatives in Europe, and hardly any in the area of data exchange. There may be good approaches on paper, and millions of euros have been invested in guidelines and concepts, hundreds of pages have been written. But so far there have been no concrete implementation projects.
Five arguments, or "common excuses", for not tackling the problem of unstructured and outdated master data for loading and unloading requirements in logistics
Instead, I often hear very similar, supposed arguments from companies as to why they are unable to tackle the master data problem. An almost universal pattern emerges. The topic of master data optimization is tossed around like a hot potato until it finally drops. Here is my personal top 5 list with my comments and tips.

- “We have an economic crisis.”
The phrase alone has a paralyzing effect and is universally applied to anything that sounds like action and change. In critical times, the pressure for cost efficiency and optimization increases. Master data is a “low hanging fruit” that can be implemented quickly and requires few IT resources. Especially when employees are spending a lot of time and effort on emails and phone calls to pass on relevant delivery information or to explain why another truck had to be turned away. Especially in times of economic stress, it is important for companies to reduce spending on non-value-added activities. This includes, for example, the manual and time-consuming processing of logistics enquiries for freight tenders. Crises are always opportunities: temporary downturns always free up labour resources. You just have to know how to use them effectively!
- “We are implementing SAP S/4HANA”
Anyone who thinks that SAP S/4HANA doesn’t need structured master data for logistics requirements is sadly mistaken. S/4HANA has the same free text fields for logistics requirements that R/3 had. If you don’t have this master data on your radar when implementing S/4HANA, you will have no information base for relevant processes in TMS or Yard Management. Just like before. So this wouldn’t be an improvement – it would just be a transfer of the (bad) status quo to a new environment.
- “We don’t need any data, our freight forwarders know everything.”
There are indeed carriers who know all the loading and unloading requirements and do not need any information from their customers. Especially not structured information. If you have such a carrier in your organization, you should cherish him because he’s priceless. However, you are likely to find that the cost is high. Because of the dependencies involved, you should not try to put your transport out to tender in this case: a change of carrier could be fatal to your transport reliability, and customer complaints would be inevitable. (And if you must, there’s probably an Excel spreadsheet or PDF document somewhere you can consult). What could go wrong?
- “We all have neither complaints about missing data nor special logistical requirements.”
Really? Every company has specific loading and unloading requirements. No company would say to the carrier: come when and how you like. At the very least, there are opening and closing times, loading point sites, registration procedures and often safety requirements. This minimum set of requirements applies to every carrier or consignee. And the more complex the industry, the more there are. Sometimes trucks are rejected because the carrier or driver didn’t know something they should have known. Demurrage charges are often incurred, schedules are disrupted and the goods have to be delivered a second time.
- “No time for master data. Let the AI do it.”
Digital projects that ignore the basics risk failure. Everyone knows that a bad analogue process becomes a bad digital process. And then AI is supposed to come to the rescue. But what exactly is it supposed to do with the data? AI solutions need structured data – they don’t make data structured. So to those who are hoping that AI will solve the decades-old problem of poor master data quality, I can only say: Hope dies last.
It’s time to roll up our sleeves. Improving master data quality in logistics is a challenge that can only be met by working together. For supply chain companies, collaboration means taking responsibility for accurate information and making it available digitally. It is time to put aside false arguments and take action. This is the only way to improve efficiency, transparency and resilience in supply logistics. Anyone dreaming of AI-assisted logistics optimisation must first clear out the graveyard of unstructured master data. Or in the words of Sherlock Holmes: “It is a great mistake to theorise before you have data. Inevitably you begin to twist the facts to fit the theories, instead of fitting the theories to the facts.
Loady is the winner of the German Startup Cup in the category Smart Logistics
Mannheim, 11.08.2024 – Great success for the Mannheim-based IT start-up: Loady wins the German Startup Cup. Our COO Elzbieta Wiankowska impressed both the jury and the audience with her pitch and secured the Startup Cup.

Photo 1: from left to right Victor Kaupe (BASF Coatings), Elzbieta Wiankowska (Loady) and Gerd Große (GFFT)
This year’s Symposium for Logistics and Production took place on 6 November 2024 at BASF Coatings in Münster. The prize is awarded annually by the Gesellschaft zur Förderung des Forschungstransfers (GFFT) under the direction of Gerd Große.
Loady, along with startups Logistikbude and s2 data, reached the final in the Smart Logistics category. Our COO, Elzbieta Wiankowska, impressed both the jury and the audience with her pitch and secured the startup trophy with 43% of the votes. This award once again shows that Loady can create added value for efficient data management in the logistics ecosystem by enabling the management and exchange of logistics requirements in a simple and structured way.
The members of the jury were Prof. Dr. Diethardt Freye, Sebastian Girle, Jörg Heitzler, Dr Thomas Schamberg, Johannes H. Schirmer.
About the German Startup Cup
The German Startup Cup, organised by the Gesellschaft zur Förderung des Forschungstransfers e.V. (GFFT), awards prizes for innovative business ideas in various categories. The competition honours start-ups that not only provide new impetus with their approaches, but also actively contribute to promoting the innovation landscape in Germany.
Further information: German Startup Cup 2023 for Production and Logistics awarded
“Digitalization as the key to efficiency” – from CHEManager 08/2024
Freight forwarder Kube & Kubenz relies on digital data and the integration of accurate master data from Loady

14.08.2024 – Kube & Kubenz relies on digitalization and, by connecting to the Loady master data platform, on reliable, digitally usable data to optimize transport planning, dispatching and communication with drivers.
Making the most of available capacity is crucial for freight forwarders. This is why the Hamburg-based forwarder Kube & Kubenz relies on the integration of valid master data from Loady. In 2023, a 9,7% drop in production in the chemical industry led to significant capacity utilization issues. As the market recovers, forwarding companies face even greater challenges. In particular, the growing shortage of drivers and skilled workers, combined with rising costs, such as the 80% increase in toll charges, is causing problems for the freight forwarding industry and the industry as a whole. Now more than ever, it is critical to maximize available resources and minimize waiting times and wasted trips.
Kube & Kubenz is an international forwarding and logistics company specializing in the transportation of liquid hazardous goods, chemical gases, and other chemicals. Konstantin Kubenz, Managing Director of the company, relies on digitalization and, through the connection to the Loady master data platform, on reliable, digitally usable data to optimize transport planning, dispatching and communication with drivers. For years, Kubenz has been active in European associations and working groups to promote digital collaboration and drive standardization and harmonization in digital logistics. “We are forced to consistently minimize manual effort,” says Kubenz. “This also means that the increasing amount of administrative work that we have taken on for our customers over the years is being put back where it belongs: with the customers themselves.” Kubenz specifically refers to all the information that needs to be considered when goods are picked up or delivered to a site. “Our dispatchers should focus on dispatching, not managing third-party data. Whether it’s opening hours, loading times, temperature requirements, safety equipment information, necessary documents, or technical equipment, each supplier and recipient in a supply chain should maintain and keep their own data up to date. As carriers, we often find ourselves or our drivers painfully aware of changes when they are unable to complete a shipment as planned or even have to return.”

"We are forced to consistently minimize manual effort.”
Konstantin Kubenz
Managing Director, Kube & Kubenz
Reduce costs and enhance competitiveness
The cost of a wasted trip runs into a four-digit range, which can add up over the course of a fiscal year. When supply chain partners maintain their own data, carriers no longer have to spend a lot of time manually managing data or documents, and there are no more miscalculations in freight tenders. “If we can save just 1% of our costs by connecting to Loady, it will directly boost our business results by six figures. We will also be able to lower risk charges, handle more orders, and improve our overall competitiveness. This, in turn, benefits our customers,” says Kubenz.
Positive impact on carbon footprint and increased satisfaction
Reliable, smooth transportation brings more than just financial benefits. A wasted trip can add between 50 and 350 kilometers to a truck’s route, with a loaded fourty-ton truck emitting between 130 and 950 kg of CO2. Faster loading and unloading also lead to increased satisfaction for both the company’s customers and their end customers, who enjoy fewer errors and greater predictability. Additionally, drivers benefit from shorter waiting times and improved planning, which they have long been seeking.
Data sharing benefits everyone in the supply chain
With Loady, manufacturing companies manage and update their specific loading and unloading requirements. This ensures a reliable source of information that benefits everyone involved, especially the companies themselves. They avoid incorrect information flows, questions, and disputes. When requirements change, the data is automatically synchronized with their business and logistics partners, keeping everyone promptly informed of the updates.
Conversely, the forwarding and logistics company keeps master data on its vehicles, drivers, and equipment in a separate digital platform. This data is then shared with customers in the supply chain, especially when they want to digitize or automate truck dispatch at their site.
For maximum benefit, Kube & Kubenz plans to integrate Loady’s data into the forwarder’s Transportation Management System (TMS). The interface is expected to be implemented in the third quarter of 2024.
Source CHEManager 08/2024: Digitalization as the key to efficiency | CHEManager (chemanager-online.com)
Loady joins Microsoft Startups Founders Hub

Loady is now officially part of the Microsoft Founders Hub for startups.
This partnership brings us closer to our goal in the world of digital logistics: "making logistics easier."
- Microsoft Founders Hub for startups supports Loady in harnessing the unlimited potential of AI through direct access to the latest AI models.
- Moreover, as partners, we receive personalized and expert guidance on AI and Cloud based solutions.
Mannheim, 20.06.2024 – Our new partnership with Microsoft for Startups brings us numerous benefits. The platform allows us free and discounted use of services like Microsoft 365, Azure, or Visual Studio. Powerful AI solutions like Azure OpenAI Service with security and compliance benefits will support and drive our efforts in optimizing and expanding our technological innovation landscape.

Abb. 1: Dennis Jantos (CTO of Loady GmbH)
“By joining the Founders Hub we are committing to our strategy to build our logistics platform on top of the Microsoft ecosystem like the Azure cloud with highest security and compliance standards to offer the best experience for our users and developers“, says Dennis Jantos, CTO of Loady.
Loady focuses on supporting transport logistics operations with reliable loading and unloading information through our “Master Data Sharing Platform.” This platform serves as a critical foundation for enhancing digital collaboration and automation within supply chains. Leveraging Microsoft Azure tools and services ensures we prioritize user-friendly experiences, bolster security measures, and promote data privacy, transparency, and trust. These elements are essential in meeting and exceeding the expectations of our customers and partners regarding service quality and reliability.
Loady dives into Artificial Intelligence
Loady’s AI transformation is just beginning. With Microsoft on our side, we are well-positioned to expand our presence in the international market. We look forward to what this membership will bring in terms of new developments and advancements.

CONTACT
Stefanie Kraus
+49 151 23712351
About Loady
Loady is an intelligent platform for standardized logistics requirements. Acting as the Single Source of Truth that shippers, goods receivers, and carriers can rely on, Loady facilitates seamless collaboration among shippers, goods receivers, and carriers through a sophisticated synchronization model. This enables true digital integration within supply chain logistics. Loady features API interfaces integrated with key logistics systems and provides multilingual online views tailored for carriers and drivers.
Moreover, Loady enhances the transport of bulk and liquid products through a central database for pre-product restrictions and cleaning requirements.
Joint Press Release: Loady closes financing round of 3.2 million euros after spin-off from BASF incubator
Digitalization of supply chain logistics: Loady closes financing round of 3.2 million euros after spin-off from BASF's business incubator

Fig. 1: Loady Founders f.l.t.r. Stefanie Kraus (CEO), Elzbieta Wiankowska (COO) and Dennis Jantos (CTO)
- The seed financing round, led by Startup BW Innovation Fonds GmbH & Co. KG and MBG Mittelständische Beteiligungsgesellschaft Baden-Württemberg, was successfully closed.
- Loady offers a master data platform that optimizes the entire B2B transport process.
Mannheim, 12.06.2024 – Loady, a cross-industry platform for optimizing logistics, successfully closes a seed financing round to further expand its business activities. The round was led by Startup BW Innovation Fonds GmbH & Co. KG and MBG Mittelständische Beteiligungsgesellschaft Baden-Württemberg and supported by Chemovator, KST Invest and a pool of private investors. Loady offers customers a master data platform on which companies can manage and use reliable logistics requirements and share them with logistics partners. The startup was recently spun off from Chemovator, the business incubator and early-stage investor of BASF.
Harmonization of data and simplified access to logistics requirements for all parties involved

Fig. 2: With Loady’s wide range of services, master data can be viewed and edited on various devices and in numerous languages.
With Loady, the founding team consisting of Stefanie Kraus, Elzbieta Wiankowska and Dennis Jantos offers a solution for the oftentimes manual, slow and error-prone flow of information in the highly fragmented logistics sector. With its secure platform and integrated add-on solutions, Loady is the first company to provide a standardized system as a single source of truth that all participants along the logistics supply chain can refer to. It is the industry itself that maintains their requirements in Loady’s common structure. This allows shippers, freight forwarders and truck drivers to access up-to-date information at all times. As a result, the chemical and automotive industries, among others, can become more efficient and sustainable in their logistics: Truck journeys that are incorrectly planned or incompletely equipped will become less and less commonplace – reliability and predictability in the supply chain increases.
“With Loady, we are eliminating a fundamental weakness in logistics. From now on, relationships between shippers, freight forwarders, truck drivers and customers will change for the better. Loady saves all logistics partners money and valuable time – and is a key success factor for further digitalization and automation,” says Stefanie Kraus, co-founder and CEO of Loady GmbH.
Taking the next steps and driving growth with strategic partners
Startup BW Innovation Fonds GmbH & Co. KG, managed by MBG Mittelständische Beteiligungsgesellschaft Baden-Württemberg, led the financing round as a financial investor. MBG draws on more than 50 years of expertise and acts as an interface between the old and new economy, opening new doors for both startups and existing companies. For Loady, MBG is a strong partner and supporter on the way to becoming a successful and profitable company in Europe and preparing the team for future expansion into the US market.
“Loady has the unique potential to become the leading master data software for logistics-intensive requirements and sectors such as the chemical industry in Germany and Europe. With its proven solution, Loady serves an extremely attractive and global market, transforms companies’ transportation processes and generates valuable data for maximum success. We are convinced of the startup’s disruptive concept and that Loady will benefit companies in Baden-Württemberg and throughout Germany,” says Andreas Stadie, Investment Manager at MBG.
With the closing of the financing round, Loady is the sixth startup to successfully spin off from Chemovator, the business incubator and early-stage investor of BASF. Even after becoming independent, important relationships between Loady and almost all BASF operating divisions as customers or potential customers remain.
“It is always a special moment for me when a venture successfully leaves us and takes own steps forwards. Loady is a remarkable startup that combines a strong founding team with many years of expertise to solve a relevant need for the entire logistics chain of the chemical industry, “ adds Markus Bold, Managing Director at Chemovator GmbH.
The financial and strategic support of the investors brings Loady closer to its goal of optimizing 60% of chemical transports in Europe by the end of 2025, reducing costs by around 500 million euros and saving over 30 thousand tons of CO² emissions. In addition, the team plans to expand the existing offering with new functions and adapt the technological framework for additional industries.
About Loady GmbH

Loady is the first platform for master data in supply chain logistics. The Mannheim-based startup was founded in 2023 out of the chemical industry to address a decades-old weakness in logistics. With its standardized data model, API interfaces and user-specific views, Loady enables effective digital communication of loading and unloading requirements, making the entire logistics process smoother, more integrated, more cost-efficient and more sustainable. In addition to the digital platform, the product portfolio also includes the Loady2Go app for drivers in a variety of relevant languages. Starting with use cases for chemical transportation in Europe and with 20 industrial sites already connected, Loady is positioning itself for further expansion into other industries and regions in the coming months.
For more information, please visit www.loady.com.
Press contact Loady
Stefanie Kraus
+49 151 23712351
About Chemovator GmbH

Loady is the first platform for master data in supply chain logistics. The Mannheim-based startup was founded in 2023 out of the chemical industry to address a decades-old weakness in logistics. With its standardized data model, API interfaces and user-specific views, Loady enables effective digital communication of loading and unloading requirements, making the entire logistics process smoother, more integrated, more cost-efficient and more sustainable. In addition to the digital platform, the product portfolio also includes the Loady2Go app for drivers in a variety of relevant languages. Starting with use cases for chemical transportation in Europe and with 20 industrial sites already connected, Loady is positioning itself for further expansion into other industries and regions in the coming months.
For more information, please visit www.loady.com.
Press contact Chemovator
Jennifer Kürner
+49 175 6406795
About MBG Mittelständische Beteiligungsgesellschaft Baden-Württemberg

MBG Mittelständische Beteiligungsgesellschaft Baden-Württemberg GmbH is one of the largest providers of venture capital in Germany. It invests in the public interest and is a partner to SMEs. It currently provides around 660 small and medium-sized companies in Baden-Württemberg with over 209 million euros in equity capital. MBG supports growth and innovation projects, company successions and start-ups primarily with mezzanine capital in the form of silent partnerships. As a fund manager, it manages several venture capital funds for institutional investors such as banks, insurance companies, foundations and the public sector, such as the Start-up BW Innovation Fund active here. MBG’s deep network in the economy, through its shareholder group of chambers, associations and the banking industry, is the starting platform for faster growth for the portfolio companies.
For more information, please visit www.mbg.de.
Press contact
Dunja Geisler
0711/1645-703
About KSt Invest GmbH
MBG Mittelständische Beteiligungsgesellschaft Baden-Württemberg GmbH is one of the largest providers of venture capital in Germany. It invests in the public interest and is a partner to SMEs. It currently provides around 660 small and medium-sized companies in Baden-Württemberg with over 209 million euros in equity capital. MBG supports growth and innovation projects, company successions and start-ups primarily with mezzanine capital in the form of silent partnerships. As a fund manager, it manages several venture capital funds for institutional investors such as banks, insurance companies, foundations and the public sector, such as the Start-up BW Innovation Fund active here. MBG’s deep network in the economy, through its shareholder group of chambers, associations and the banking industry, is the starting platform for faster growth for the portfolio companies.
For more information, please visit www.mbg.de.
Industry and logistics: Master data platform Loady helps optimize supply chain and saves costs
The Mannheim-based startup Loady has built and launched a master data platform as a cross-industry solution to enable the binding exchange of loading requirements along the entire supply chain. Companies using Loady keep their site- and product-related logistics requirements up-to-date in Loady and share their data securely with their business and logistics partners.

Modern logistics processes should be as cost-efficient and fast as possible, which is why loading and unloading trucks at manufacturers and their customers are closely timed. Crucial to a smooth process is the exchange of information on loading requirements. Until now, companies have maintained the relevant requirements for loading at their sites and unloading at customers’ sites differently. As a result, each company must keep all information from business partners up to date in its own systems. This information is then passed on to logistics partners – usually in a free text format. It is then up to the partners to identify and implement the relevant information themselves. Because the texts are unstructured and not standardized, they are not suitable for digital collaboration along the supply chain. Stefanie Kraus, co-founder and CEO of Loady describes: “Especially at industrial sites in the chemical industry, there are so many different things to consider when it comes to loading and unloading trucks. With Loady, we help simplify and standardize the entire logistics process, from freight purchasing and freight ordering, to transport planning and scheduling, to the transport itself.”
The Petrochemicals division of BASF SE in Ludwigshafen is already using Loady’s service. There, larger freight tenders require some effort in preparation, including manual verification steps of the freight data and requirements to be transmitted. Nevertheless, it happens time and again that loading requirements are not fulfilled. In addition to avoidable costs, this causes extra kilometers and unnecessary CO2 emissions. “By managing our master data on loading requirements in Loady from now on, we want to make our logistics more plannable and reliable,” says Jochen Roll, Supply Chain Manager of the Petrochemicals division at BASF SE. “By using Loady, we are also enabling our logistics partners to meet our expectations and those of our customers – while saving costs and gaining planning reliability themselves.”
In addition, processes are being simplified at other points. “From the point of view of digitalization and automation in logistics, the previous way of doing things is also outdated,” says Stefan Ritschel, Vice President Supply Chain Management and Digitalization in the Petrochemicals division at BASF SE. Customer service, product management and experts at the loading points are currently working flat out on data collection. As early as this fall, freight tenders for the first 500 products of the Petrochemicals division are to be mapped with data from Loady. By 2025, the Europe-wide transports of more than 4,000 products are to be organized and thus optimized via Loady together with other BASF divisions. “This is the first time we have a reliable source of loading requirements that we can access from a wide variety of systems, whether it’s in the freight order, checklists, online views or through direct integration with our enterprise systems,” Ritschel says.
For goods receivers who want to maintain their locations in Loady and share them with their suppliers, Loady is accessible as a free service.
About Loady
Loady is a cross-industry master data platform that enables loading requirements to be communicated smoothly along the supply chain. Truck drivers can directly access delivery-relevant information in German, English, Polish and Spanish free of charge via the online view “Loady2Go” (in translation: Italian, Romanian, Russian). All parties in logistics – companies and freight forwarders – can refer to Loady as an authoritative source.
Loady was designed and developed since 2021 at Chemovator, the business incubator of BASF, as a neutral, cross-industry, standardized platform. Loady is suitable for inbound and outbound transportation of bulk and packaged goods. The spin-off of Loady as an independent GmbH is planned before the end of 2023. For more information, please visit: www.loady.com
The clear end to truck waiting times and delays at gates and loading ramps
Loady2Go makes up-to-date loading information understandable for truck drivers and available online in their language.
- Loady, the new master data platform for loading requirements, launches Loady2Go
- Truck drivers can call up delivery-relevant information in their language via a link or QR code
- Loady2Go aims to reduce waiting times and increase truck driver satisfaction. But also to save costs, empty and extra kilometers – and thus CO2 emissions.
Loady, the cross-industry standard platform for loading requirements, now offers a fundamental improvement for transports along the supply chain. With Loady2Go, truck drivers can view all delivery-relevant information directly online – and understandably and in their own language.
Loady2Go aims to solve a ubiquitous problem in the transport industry. Because incidents occur again and again and the supply chain suffers from it – but especially the drivers themselves. A typical situation: the truck driver arrives at the destination to load or unload goods, perhaps even within the reserved slot. However, there is still a lot that can go wrong now for a smooth process. Ignorance regarding the applicable requirements, unclear information and, last but not least, language barriers lead to misplanning and misunderstandings time and again – and thus to truck rejections and delays. No wonder, given the multitude of things that need to be considered: documents, safety equipment, processes and procedures, certifications, technical equipment, contact persons, delivery times and much more.
Every incident at gates and loading docks means waiting and idle times, phone calls, emails, troubleshooting, and therefore unnecessary delays, costs and frustrations.
Loady2Go aims to fundamentally simplify transportation with clear information and avoid misunderstandings and mistakes. With Loady2Go, drivers always have all delivery-relevant information at hand on their smartphone or tablet. A link or QR code in the freight order takes them directly to an easy-to-understand online view. Registration is not necessary. Loady2Go is available in German, English, Spanish and Polish. Italian and Ukrainian will be added soon, with other European languages to follow.
To improve the overall “Driver Experience”, in addition to the usual contract-related requirements, Loady2Go also includes information that enables the driver to find his way around on site in the best possible way. This includes, for example, important information on parking options, truck access, infrastructure and service facilities.
Loady2Go wants to make drivers’ lives easier and transports more plannable at the same time. The goal is also to counteract the existing driver shortage. Today, one in ten driver positions is already unfilled, and 2 million vacancies are expected in Europe by 2026.
Loady is not alone in this. The industry is currently taking a variety of approaches to treat drivers with more respect and provide a better infrastructure for them. This also includes simplifying communication and facilitating interactions at the interfaces. This is also demonstrated by initiatives such as the “Facility Rating App” from Uber Freight, the “Driver Feedback App” from the European Chemical Transport Association (ECTA) or the desire of DOW Chemicals to be a “Golden Choice Site”.
Online driver views Loady2go can be created by customers of the platform Loady – companies from industry and trade, but also logistics service providers. For truck drivers, the use of Loady2Go is not associated with any service fees.
About Loady
Loady is a cross-industry master data platform that enables loading requirements to be communicated smoothly along the supply chain. Loady supports and simplifies the end-to-end logistics process, from freight purchasing, freight order, transportation planning and scheduling, to actual delivery. Companies maintain their location and product-related requirements in Loady and then share them securely with their business partners. Loady (loady.com) is a venture of Chemovator GmbH, the business incubator of BASF
Website: www.loady.com
Loady product-market fit confirmed by international jury
Loady addresses a core issue in industry and logistics – and has impressed the international IFOY jury as well. The confirmed product-market fit proves: this solution strikes a real chord in the market.

IFOY Innovation Check: LOADY, Loady
Kategorie: Start-up of the Year
Market relevance
LOADY’s product named Loady addresses the enormously important issue of standardized data exchange in the awarding and execution of transport orders in the forwarding environment, both in the industrial and the commercial environment. It thus provides “standardized and reliable requirements for loading and unloading at industrial sites” – undoubtedly a highly relevant problem for an extremely high number of companies today. There is almost no manufacturing company or trading company that is not affected by the issue.
Customer benefit
Standardized data storage and maintenance are already an enormous lever for error prevention. If necessary, this data is then also exchanged automatically and standardized on a case-dependent basis. This eliminates significant causes of errors and significantly increases process reliability. This does not only offer an advantage when all contractual partners of a process use the system, but already when one of the contractual partners has it in use, the first important advantages already become usable, through the then as free text, but nevertheless structured and standardized as well as previously checked provision of the data.
Novelty / Innovation
The problem, which is actually of far-reaching relevance, has simply not been addressed to date; it is the first solution of its kind. The market behavior regarding the acceptance of data handling has not yet been fully clarified. The usability on the basis of different clients allows the product to be quickly implemented and accepted by users. The standard must be accepted as such by those responsible for the company.
Functionality / Type of implementation
The product is implemented with a convincing architecture, which also provides suitable clients with easy-to-use functionalities for the different user groups. Particularly is the conception, which already makes a significant advantage convertible also with initial few users. This makes a possible successful implementation profitable even in the initial phase for individual customers – a topic that is unfortunately often neglected in many products.
Verdict
At the interface between supply chain and intralogistics, this start-up is positioned in the area of loading. “The future standard” (own statement) offers a structured linking of data to optimize the overall process of freight from tendering to ramp approach. In addition, there is an architecture of applications up to an app for the driver. The challenge here is whether the proposed structure will actually be accepted as a new standard by stakeholders. However, the product can also function on its own, without another company being connected, and then outputs the data as free text, but in an optimized structure.
IFOY Test Report: LOADY, Loady
Category: Start-up of the Year
Loady is a Software as a Service (SaaS) solution and industry-wide reference source (single source of truth) for loading and unloading requirements that all logistics partners in the supply chain can refer to. For the first time, shippers and consignees can enter all the information and requirements that need to be considered for loading and unloading a truck at their location and for specific products into a standardized data structure.
The software includes a modular data model that can be used for complex, large sites and hazardous goods, as well as smaller and simpler goods deliveries. By assigning transport lanes, data can be shared with business and logistics partners for the respective operational processes. Data changes are tracked in the software, and there is a data history. This means that it is always possible to see which data status was valid at which point in time. Authorized business and logistics partners can be informed directly in the event of changes to relevant data fields. The data is used in the company applications via API, and there is also a mobile, multilingual interface for drivers.
There is no predecessor, just a long-standing breaking point that can be overcome with the software. Loady is the first solution on the market to manage loading and unloading requirements in a structured data model and be a reliable source for all logistics partners. The software is also the first centralized pre-product database.
Loady thus offers a meaningful alternative to free-text fields, in which companies currently try to track their requirements for loading, but also for unloading at their customers, in continuous text format, laboriously and sometimes incorrectly. In SAP, this mainly concerns the fields G12 and G14 in the forwarding orders. The software can also be used to replace manually compiled Excel files for logistics tenders, cleaning requirements and preliminary products.
Loady is relevant for all supply chain companies and their logistics service providers, Europe-wide and globally. This means a market volume of over 60,000 medium to large industrial companies and more than 20,000 logistics service providers worldwide.
IFOY test verdict: Industrial companies and logistics service providers benefit from Loady by providing reliable master data that is used along the processes. Responsibilities for relevant information are clearly defined. This is ensured by established data management roles with clear data governance rules. As a result, the risk of trucks being rejected at the loading or unloading point is also a thing of the past. In this way, the software helps to avoid extra or empty kilometers (reduction of carbon dioxide emissions). The effort required for problem solving, root cause clarification, data maintenance and mutual verification of information is reduced. Relevant changes are automatically communicated to business and logistics partners. This is associated with increased responsiveness, which leads to better understanding among all parties involved. Overcoming language barriers through a multilingual interface with direct translation for data managers, drivers and freight forwarders also contributes to this.
Digitalization of logistics: Loady provides a unified platform for (un-)loading requirements
The IT startup has managed to effectively solve an essential problem in the entire transport logistics. Using only one single source the industry and logistics service providers are experiencing a new way of handling their loading requirements, efficiently.
In today’s rapidly evolving digital landscape, small & medium-sized companies as well as large corporations must overcome a wide range of challenges. They need to know how to be successful and stay competitive in the global market. Using software and technologies to automate business processes and functions can become a key factor in order to differentiate own products and services from their competitors.
Different types of information sources are disabling the digitalization in logistics
While other industries keep up with digital transformation of their businesses, logistics is still mainly driven by manual processes. Up to 5% of trucks are rejected due to unclear or unknown requirements.
Shipping companies, logistics service providers and goods consignees are the first ones suffering the consequences. Digital transformation has been the major logistics challenge of the last 10 years. The digitization of the entire supply chain provides logistics partners with the latest digital solutions to fundamentally improve their visibility into operations. For example, using Track & Trace or IoT- and AI apps for freight procurement and freight planning. There are different channels used to communicate data between shippers and carriers. However, for purchase orders, shipping notices, invoices, or any documents to be exchanged still prevail EDI tools, that replaced paper-based documents about 20 years ago. Since decades, logistics runs via phone, email, fax and spreadsheets – a fact that still remains in 2023. The digitalization of the entire B2B logistics is progressing slowly compared to other industries. According to the Economy index DIGITAL logistics ranked only second to last place.
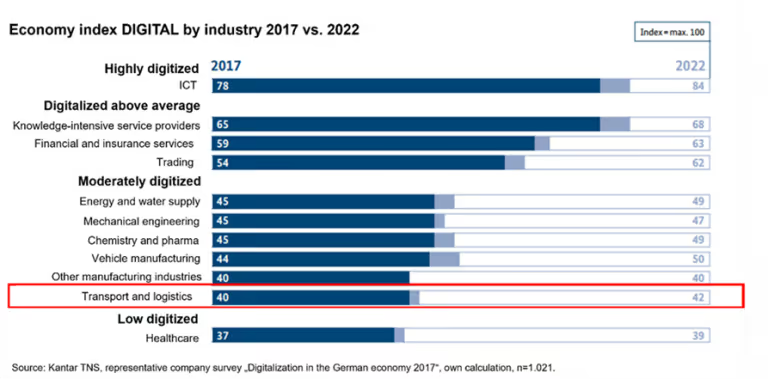
Fig. 1: Economy index DIGITAL 2017 vs. 2022.
One of the key factors that is slowing down the efficiency of transport logistics in terms of successful cooperation, higher reliability and planning capability is a lack of appropriate communication. Contract and transport-relevant (un-)loading requirements are still managed in unstructured freetext fields and communicated inefficiently.
Some examples: a truck arrives during the opening hours of the gate, but too late for unloading at the particular loading point. Required technical or safety equipment is missing. The carrier hasn’t brought a suitable pump or simply some documents necessary for receiving products are incomplete. The reason for these defects to happen is simple: inaccurate or obsolete information. All parties – shippers and carriers – are trying to keep up with the relevant requirements in their own way. There is no clear data and no clear communication. Consequently, troubleshooting and never-ending discussions about truck specifications, local procedures and other restrictions occur daily. Generally, logistics partners make use of what they know and not of what is sent, because they don’t trust the information. That means, that in the worst case they have received updated requirements, but do not believe they are valid. At the end of the day all parties involved are faced with continuously rising costs, more delays, frustration, extra and empty kilometers. This is exactly why we have developed Loady and built together with logistics experts a platform that makes (un-)loading processes cost-efficient and sustainable.
A standardized platform for (un-)loading requirements finally enables transparent logistics
Loady optimizes the entire B2B transportation process: from freight procurement, freight ordering, transportation planning and dispatching, to actual delivery. Companies maintain directly in Loady the requirements to be followed for loading their sales products or unloading the products delivered to them at their sites. By means of temporarily limited assignments, they share the information necessary for the operational process with their business and logistics partners.
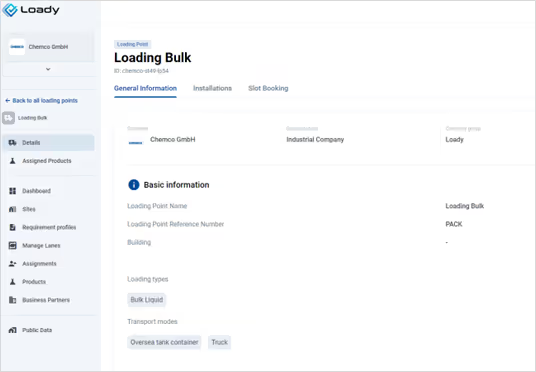
Fig. 2: Maintaining requirements in Loady, here: access restrictions for loading bulk products
Loady simplifies the requirements’ management also for logistics service providers. Companies are providing their partners with valid information on (un-)loading requirements, informing automatically about any process changes. Doing logistics this way makes all parties involved happy, because misunderstandings don’t arise at all. This translates directly in less truck rejections, less delays and troubleshooting, increased planning capability and an easier life for the drivers
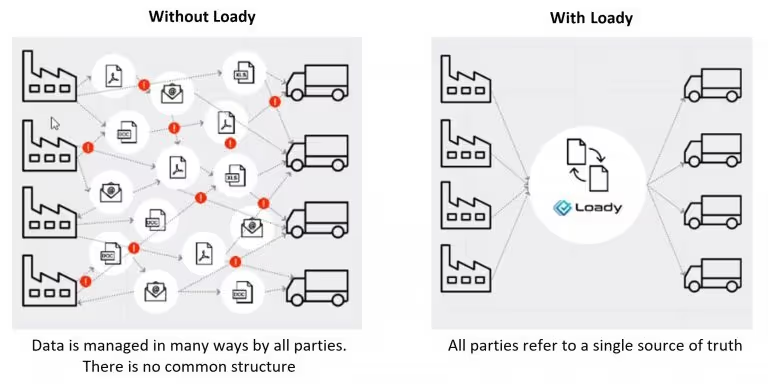
Fig. 3: Handling loading and unloading requirements in the logistics, with and without Loady
With Loady, relevant and updated (un-)loading requirements are always available. The standardized platform offers different modules according to the different customers’ needs. An intuitive user interface and a clear structure support them in handling their data efficiently – decreasing costs and increasing efficiency. With Loady API, companies can integrate master data from their systems to Loady, enrich the data there with additional attributes – e.g. pre-product or site logistics specifications – and then get a full, up-to-date data set automatically back to their systems for further processing. Today Loady is available in different European languages – German, English, Polish and Spanish. Loady keeps growing and therefore will be introducing in future another languages as well.
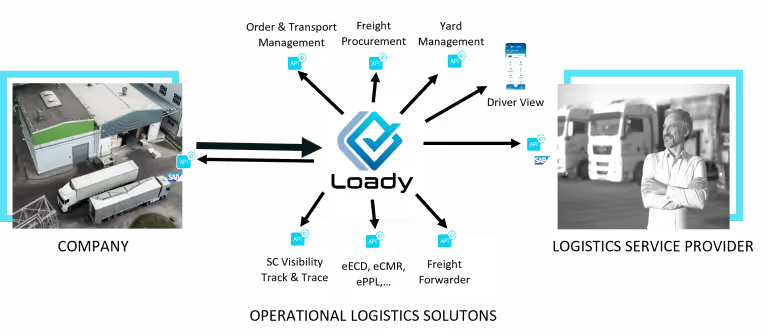
Fig. 4: Reliable and up-to-date loading requirements used in processes are available on the interoperable platform Loady
Via mobile view Loady2Go, drivers can access updated (un-)loading requirements in a comprehensive way and switch the language with one click. This makes it much easier to manage deliveries even to new places and prevents unnecessary waiting times and (un-) loading incidents.
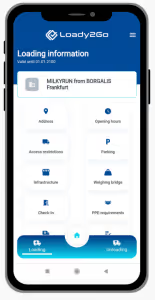
Fig. 5: Multilingual Driver View Loady2Go
The vision behind Loady is simple: we want to help companies and carriers all over the world to improve their logistics processes by communicating clear information more efficiently along the supply chain.
A Venture of BASF is becoming the industry-wide standard for logistics data
Loady is a venture of Chemovator GmbH, the business incubator of BASF. After first conversations and workshops with internal and external experts in logistics and chemical transportation, the idea of a centralized platform and place to go for valid information was born. “We would have never imagined that there were still so many manual processes, break and pain points in logistics processes,” so Stefanie Kraus and Elzbieta Wiankowska – both co-founders of Loady and former employees of BASF SE. Despite digitalization, master data used in logistics is managed the same ways for the last 25 years. In 2021 they pitched their idea of Loady at Chemovator, the business incubator of BASF. The jury noticed immediately the potential of Loady and the impact that such a platform would have on the entire industry. So, they started to build the solution.
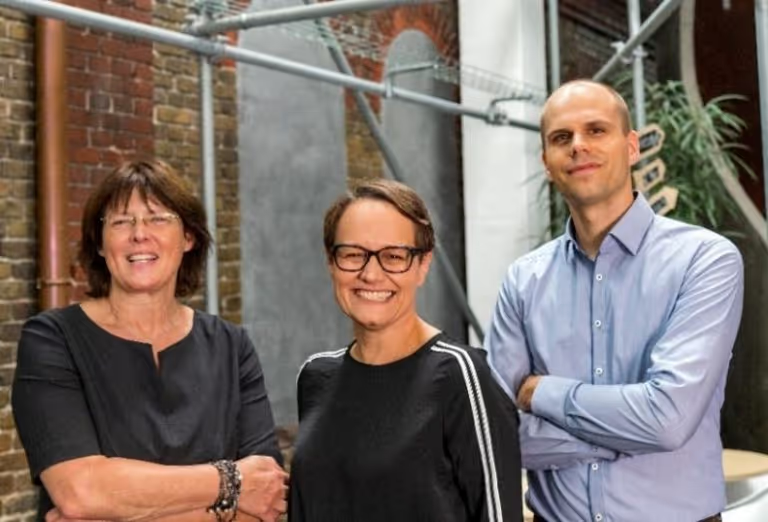
Fig. 6: Co-founders of Loady Stefanie Kraus (CEO), Elzbieta Wiankowska (COO) and Dennis Jantos (CTO)
During the pilot phase in 2022, BASF and Evonik were the first industrial companies to test Loady with several bulk and packed product transports. Also logistics service companies like Bertschi, Lanfer and Talke participated in the pilot. Meanwhile, more than 20 European industrial sites, 30 (un-)loading points and 150 products to be transported are onboarded. In September 2023, Loady will spin off as an own company.
An innovative approach developed for the chemical industry is about to become an industry-wide, standardized, digital platform for logistics, globally.
About Loady
Loady is an industry partner platform that enables an effective and seamless communication of loading and unloading requirements along the supply chain network: from logistics procurement to freight order management, planning and dispatching, up to the physical delivery of goods.
In Loady, companies can maintain their site and product specific specifications in a standardized data structure, and then share them with their business partners and carriers in a secure way. Loady provides a multilingual driver’s view, but companies can also connect to their systems and bring up-to-date requirements directly into the specific operations and processes.
Loady improves the overall supply chain collaboration, helps to avoid truck rejections, and makes transportation services more efficient, reliable and sustainable. Loady is key success factor to further digitization and automation in logistics.
Loady (loady.com) is a venture of Chemovator GmbH, the business incubator of BASF
Email: info@loady.com
Web: www.loady.com
Transport Logistics 2023 – Loady was there!
Great impressions at the fair
The Transport Logistic in Munich from May 09-12 was a complete success! Every two years the international trade fair for logistics, mobility, IT and supply chain management takes place.
This year also with Loady!
Thank you to all visitors and listeners for your interest and the exciting conversations! For us, it was great to hear first-hand about the problems companies face with loading requirements in logistics and how this affects collaboration in transport logistics. Once again, it was evident how many costs are incurred as a result and how tedious the following troubleshooting is.
Panel discussion with Loady, DB Schenker, Transporeon and Warsteiner
In the panel discussion around innovations in logistics, our co-founder Elzbieta Wiankowska described the pain points in dealing with loading requirements in the form of long prose descriptions in continuous text. In the round with Erik Wirsing (VP Global Innovation DB Schenker), Stephan Sieber (CEO Transporeon) and Daniel Küster (Supply Chain Director Warsteiner), it became clear once again how important effective and structured data management is and what it takes to communicate it reliably. Shippers, industry and the logistics sector need to work even more closely together in this regard so that work can be done more effectively at the interfaces. Thanks to BVL for inviting us to the panel discussion!
Start Up Pitch at the Campus Plaza
At the Start-Up Pitch at the Campus Plaza, Elzbieta was able to present Loady’s ideas to a large number of interested parties and show the added value Loady brings to transport logistics in subsequent demos.
We are already looking forward to the next event and are excited about more great conversations and discussions!


Loady nominated for ifoy awards 2023
Meet and test Loady on March 29-30 at Messe Dortmund
We are proud to announce that Loady has been nominated for the ifoy awards and will be tested during the test camp intralogistics at the Messe Dortmund by an international Jury.
We are already looking forward to their expert feedback and to the opinions of all professionals visiting our booth!
Nominated in the category “startup”, we will demonstrate how all logistics partners benefit from the reliable master data that Loady provides. Clear information that helps to avoid misunderstandings and truck rejections are of special relevance in intralogistics, as they help to improve process efficiency and reduce costs. No matter if the data is needed in Yard Managment Tools or to support truck execution processes at gates, Loady is easy to manage and brings up-to-date requirements to the users where they are needed.
Finally, trucks will bring everything the need to be loaded without any problems and transports can be planned according to opening hours and processes at gates. Drivers will be prepared to manage much better at industrial sites, starting with everything needed to ensure safety and security: equipment, tests and indications.
View our nomination for the Award!
Come and visit us there!
2023, March 29-30
Messe Dortmund
If you are an expert in supply chain and logistics and still have no visitor pass for the ifoy-Awards 2023, get in touch with us!
Loady in Polish
Nasz specjalny prezent świąteczny dla wszystkich polskich kierowców

“Making the job of the truck driver more attractive” is the strategy with which industry and logistics service providers want to counteract the drastically increasing shortage of drivers. In particular, initiatives that help to reduce long waiting times and ensure the smooth running of end-to-end transport processes are in the foreground.
Communication plays an important role here, because transports are generally provided by third-party service providers, but often passed on to other subcontractors. This means that relevant information must be reliably communicated between different parties. In the end, however, there is always the truck driver, who is expected to find his way around the local conditions and the company-specific processes: he is supposed to know what, when, where and how to manage everything in the right way. Whether it’s about opening hours, correct parking, rules on site, the safety equipment, the technical equipment or the documents to be included.
The challenge for the drivers is immense. They often do not speak the national language of shippers or customers or only rudimentarily – and the trend is rising. In addition, their field of application is diverse and usually includes customers and deliveries of different nature throughout Europe – and extremely complex industries, such as the chemical industry.
For Polish truck drivers – according to the Federal Association of Road Haulage, Logistics and Disposal BGL they make up the majority of truck drivers in Germany with almost 10% – life is now easier! Just in time for Christmas, Loady launched a new version that allows Polish carriers and drivers to access all requirements and information relevant to the planning and execution of a transport in their own language. Finally, checks at the gates or the loading and unloading points will no longer hold surprises and the probability decreases that something is missing and there will be long waiting times and exhausting troubleshooting.
What does that look like exactly? – See for yourself: Loady Driverview
About Loady
Loady is an industry-wide partner platform that enables loading and unloading requirements to be seamlessly communicated along the supply chain. Loady simplifies the entire B2B transport system, from freight purchasing to freight order, transport planning and scheduling, to the actual delivery.
In Loady, companies maintain their location and product-related requirements and then securely share them with their business partners. Loady offers a multilingual view for drivers. However, companies and logistics partners can also integrate Loady’s current data directly into their operational systems and processes.
Loady improves collaboration in the supply chain, helps minimize truck rejections, and increases planning security and sustainability in transportation. Loady is a fundamental building block for the further digitization and automation of logistics.
Loady (loady.com) is a venture of Chemovator, the business incubator of BASF.
The spin-off of Loady as a neutral GmbH is planned for May 2023.
Now it's official: Loady is a game changer
The problems that Loady is finally solving were already known 35 years ago. “Auf Achse”, a well-known board game from the 80s, allowed the team to experience many of the frustrating experiences in transportation first-hand.

Last Monday, Dennis Jantos, Elzbieta Wiankowska, Waldemar Waigel and our new colleague Vicente Manuel Suárez Silva played a game of “On the Move” after work. The classic board game — Game of the Year 1987 — is about transportation services and trucks. For us, this is an interesting opportunity to explore the feeling of road freight transport in the 80s in a fun and relaxed way.
What is “On the Move” about?
To win the game, you must make the biggest profit by accepting and completing transport orders. In order to fulfill the orders, you send your truck off to pick up goods. He then delivers the goods to the cities that are named on behalf.
But the road to successful delivery involves obstacles such as traffic jams, blocked roads and the actions of other players. Just like in real life, there are random events that have positive or negative effects on the outcome of the game.
The event cards in particular show that decades-old problems in the logistics sector are more relevant today than ever before.









Change the Game: With Loady, you run into fewer problems and become more efficient
With “Auf Achse”, we made surprising observations and it was a great feeling that we were bringing a fundamental improvement to the industry with Loady. In fact, it will never be the same again: the negative effects of the event cards would not happen this way with Loady, while the positive events represent a normal, not even significant occurrence.
“Win an extra turn”: Quick loading success factor
Fast charging increases transport efficiency, reduces truck downtime and makes it possible to carry out more trips with existing resources. We knew that back in 1987.
What is astonishing is that in 2022, the most common reasons for many truck rejections are still the following:
- No really reliable sources for up-to-date and verified information about (unloading) at the destination of transport
- Lack of documentation or equipment and, as a result, unnecessary waiting times
- Manual troubleshooting and finding solutions: by email, telephone, fax, involving 14-16 people in extreme cases
- Communication difficulties and misunderstandings due to language barriers
Benefits for shippers, customers and logistics service providers
Loady counteracts the above mentioned reasons for delay. And in a very simple way: Loady is a platform that is maintained by shippers and customers and makes reliable, up-to-date information on loading and unloading requirements easily accessible.
Loady is a standard in industry and simplifies the entire transport system, from freight purchase to freight order, transport planning and scheduling, to actual delivery.
“Go 1-3 additional fields”: Highly motivated drivers through better information and organization
One of the current main problems facing the logistics sector is the increasing shortage of drivers. There are already 450,000 truck drivers missing in Europe, a number that will double or even triple over the next 5-10 years.
The main reasons are poor working conditions, waiting times and the high level of frustration when dealing with organizational aspects of the job.


Loady makes the driver's job attractive again
Loady communicates the requirements of the respective locations at an early stage. This includes information in particular, which may not be relevant to the contract but is extremely important for local drivers. Where can I park, what facilities are there, what are the processes at each gate and establishment? Loady now provides drivers with the “Loady2Go” mobile view. Loady also overcomes language barriers, as it is already available in various European languages. This means fewer waiting times and fewer unexpected events — and, of course, fewer nerve-wracking clarifications and discussions with site personnel or plant security. Overall, the potential for frustration for the driver and everyone else involved is drastically reduced.
Bonus order: Because of your good reputation for timely and smooth delivery, your customer directly places an additional order with you
With Loady, there are fewer rejections: companies and freight forwarders increase their reliability.
If you gain the trust of your customers as a supplier or logistics service provider, that means in most cases that you will receive more orders. With Loady, your company is more trustworthy and reliable than your competition. Your customers will want to work with you. This goes hand in hand with more cooperative business relationships and more attractive pricing options.
After three games, “Auf Achse” taught us a few lessons:
Loady helps all partners in the logistics industry: Drivers are more motivated by better organization of processes; transport service providers can carry out their transports more reliably through faster and easier loading and unloading, while making more optimal use of their resources. Customers and supply chain managers receive more timely and reliable deliveries.
In the 1980s, there was no solution to these problems. Only with increasing digitalization can a platform like Loady enable such an interaction of business and logistics partners.
If Loady had existed as a standard 35 years ago, there would be other event cards and other random factors for “On the move.” The entire logistics sector would be better interlinked and the efficiency of logistics processes would be higher.
For our team, it was valuable experience that our product solves challenges that were identified decades ago and we are now more than ever convinced that Loady is changing communication in the entire logistics industry for the better and that the platform itself is becoming an international standard.
Loady goes live!

Finally, the decade-old problem of relevant information hidden in free text fields and in people’s heads is solved: Loady 1.0 is released. From now on, companies can maintain their site-specific and product-related logistics requirements in an adequate platform and then securely share their data with business and logistics partners along the entire transportation process: from freight procurement, freight ordering, transportation planning and dispatching, to actual delivery.
Loady is a single source of truth for logistics requirements to shippers, carriers and customers.
What’s in for industrial companies?
Loady offers companies a unique platform to enter and maintain company’s logistics requirements and to build end-to-end transport lanes connecting their products to the loading points at theirs sites with the unloading points at the customers’ sites.
Then they can assign their logistic service providers to the respective data sets of a lane.
Feature overview:
- Standardized data model with modular approach fitting needs of small companies, large industrial and even complex chemical sites and parcs
- Intuitive user interface to enter more than 100 requirements in a clear structure: from site restrictions, parking instructions and opening hours to safety instructions, logistics equipment and processes to follow.
- As a special Goodie for bulk transportation Loady contains a central data base for managing preloading restrictions and cleaning requirements.
- Predefined value selection, reducing any kind of free texts to an absolute minimum
- Multilingual data base: German, English and Polish are already available. Spanish follows in December, others to come in 2023
- Possibility to manage customer’s requirements while they are not managed by the customers themselves
- Create order-related access to driver view “Loady2Go”
- Communicate changes to business and logistics partners
- Integration with ERP / TMS / Yard Management via API
What’s in for logistics service providers
With Loady, for the first time in logistics, carriers will be able to get precise information on logistics requirements directly from their customers.
- Access requirements of authorized transport lanes
- Create order-related access to driver view “Loady2Go”
- Integration with ERP / TMS via API

Use cases supported by Loady:
- Logistics tender management and service offering
- End2end understanding of requirements for easier dispatching
- More flexibility to deploy drivers, independent from their language skills & knowhow
- More reliable service execution at higher quality
Clear rules for data ownership and governance
Loady is a neutral and secure partner platform where companies can manage and exchange logistics requirements. In Loady, data is owned and governed by the companies themselves. Data protection applies the rules of GDPR, data security follows the standard of ISO 27001.
Achievements of our pilot phase
Starting the Loady pilot phase in June 2022, the first industrial customers like BASF and Evonik entered by now more than 20 European sites, 30 loading and unloading points and 25 products.
Now they are building their first transport lanes and assigning them to their logistics service providers to test Loady2Go.
The first API integrations with their Transport Management Systems and Yard Management Systems are planned to take place in Q1 2023.
Future roadmap
The Loady roadmap is being defined very closely together with an expert user community assigned by our industrial and logistics customers. Beside the constant evaluation and improvement of Loady, further features that are designed to make the basic processes even easier to use.
Coming soon:
- Automated notifications in case of changes
- Change history
- Preproduct data base advanced
- Chemical Park tenant
- Loady plugin
- Carrier feedback
Want to see how Loady works?
View the recording Loady V1 (link to youtube) of our CPO and Co-Founder, Elzbieta Wiankowska.

About Loady
Loady is a standardized platform for reliable loading and unloading requirements. By enabling the effective communication of logistics specifications along the supply chain network, Loady optimizes the entire B2B transportation process: from freight procurement, freight ordering, transportation planning and dispatching, to actual delivery.
The idea of Loady is simple: companies maintain their site-specific and product-related logistics requirements in Loady and then securely share them with their business and logistics partners for their respective operations. Of course, industrial companies and logistics service providers can also access Loady via API. This allows them to integrate reliable logistics requirements from Loady directly into their operational systems and processes.
Of special interest for liquid bulk logistics is the long due solution of a general, centralized pre-product database where cleaning instructions and pre-loading restrictions can be managed and shared.
Loady fundamentally improves supply chain collaboration. Loady helps minimize truck rejections and increases planning reliability and sustainability in transportation. But above all, by providing a single source of truth for requirements, Loady will, finally, end the current practice of back-and-forth phone calls, data double checks and continuous troubleshooting that all parties involved are suffering from.
Our platform closes a fundamental gap in communication, making it a key success factor for further digitization and automation in logistics.
Ready to take the next step?
Book a demo or start for free.
Get in touch with us
Ask all questions and get an idea of the potential for logistics processes in your company.

Create your site and share data - it's free of charge!
Set up your site in just a few minutes and share your general site information directly with suppliers and logistics partners - it's free of charge.
Clear indications, fewer clarifying questions, greater efficiency!