How the supply chain in your industry benefits from Loady
Fewer misunderstandings, clear and multilingual loading requirements, standardized formats and content — and all of this can be used digitally and integrated into logistics systems. This is win-win - everyone benefits from correct data and information. Consequently, the entire logistics process becomes more efficient and plannable, from freight procurement to quotation and order management — and, of course, delivery and truck execution. Loady's central, standardized and networked data source for loading requirements makes this possible.

Shippers, consignees and logistics service providers refer to Loady as a central data source for loading and unloading requirements.
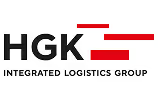
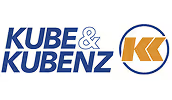
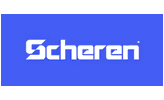
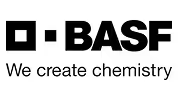
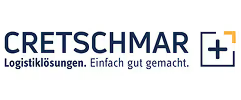
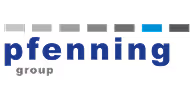
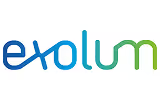
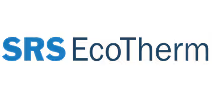
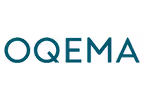
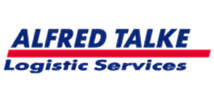
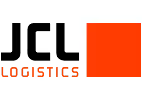
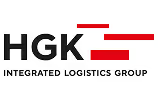
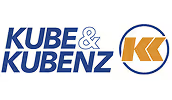
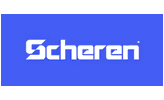
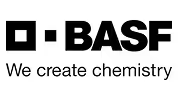
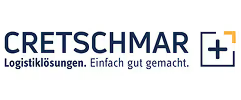
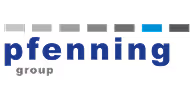
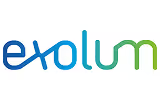
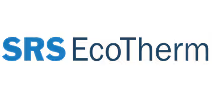
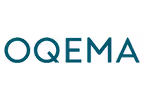
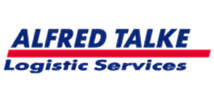
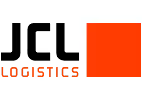
Mastering the challenge of "loading requirements" in waste-logistics
Different instructions for hazardous goods, hazardous waste, residual materials, and recyclable goods complicate communication, especially with drivers.
Lack of standardized loading requirements for each facility or location (e.g., ramp access, opening hours, safety instructions).
Different processes at municipal, private, or industrial waste disposal companies lead to misunderstandings and poor planning.
For facilities that are part of critical infrastructure (CRITIS), training drivers and external workers is very time-consuming.
Costs rise due to unnecessary waiting times and delays.
Visual and multilingual driver briefings enable easy communication regarding the requirements of different deliveries or pickups.
Standardized, unambiguous designations for loading requirements are available.
Digitally available information provides clarity – regardless of which waste disposal company is involved.
Waste and energy plants provide digital training for drivers and external workers, saving time and effort.
Valid and understandable information reduces unnecessary waiting times and delays.
Loady use cases from logistics at energy and waste plants (extract)

Less incidents and delays through simple driver briefings at the entry gate
Greater safety and fewer incidents: Truck drivers quickly find their way around with the help of easy-to-understand, multilingual driver instructions.

Complying with CRITIS
There are two ways to comply with the obligation to provide proof of driver training: manually by verifying the list or integrated via the yard management system.

Mobile and step-by-step
Whether waste, white lime, or ammonia water is being delivered or residual materials are being collected, new drivers in particular need to know immediately which steps to follow and how to operate which devices. With their own smartphone or tablet or one provided by the operator, they have everything they need at their fingertips, step by step.
Mastering the logistics challenge "loading requirements" in the automotive industry
Delays in transport jeopardize tightly scheduled production processes.
Unclear addresses and access restrictions (especially at large OEM plants) often cause misunderstandings and generate delays.
The large number of parties involved makes cooperation in logistics difficult: OEMs, suppliers, logistics service providers, warehouse operators, freight forwarders
Different IT systems, formats, and standards generate media discontinuity and hinder further digitization and automation.
Sensitive components that require special handling or technical equipment make it difficult to select new service providers or drivers.
Valid and structured information reduces the risk of incidents and delays during transport.
Clear delivery addresses and geocoordinates, opening hours, information on necessary equipment, etc. enable quick and easy access controls.
All stakeholders benefit from standardized, up-to-date, multilingual master data on loading requirements.
Different logistics applications and systems obtain loading requirements from the same source and in a uniform format.
New carriers and drivers are quickly onboarded, as they have all the necessary information and instructions available in their language and up to date.
Loady use cases from logistics in the automotive industry (extract)

Less delays trough clear loading requirements
Relevant loading and delivery requirements (e.g., addresses, vehicle restrictions, necessary equipment, ramp, slot booking, etc.) are standardized and can be accessed centrally.

Better collaboration with OEMs and tier-suppliers
All parties involved in the supply chain have access to uniform, verified master data. Manual maintenance of loading information in different systems or Excel lists is no longer necessary.

Cost savings through efficient logistics
Clear, standardized loading requirements reduce manual coordination, waiting times, and unnecessary trips—saving demurrage charges, personnel costs, and avoiding unnecessary additional mileage.
Mastering the challenge "loading requirements" in construction
Complex coordination with freight forwarders and drivers due to changing conditions and access routes as construction progresses.
Trucks get lost or end up in inappropriate places and block other processes.
Truck drivers confuse dumpsters and load or unload incorrectly.
The truck cannot unload because the driver did not know that there was no ramp.
The truck driver unloads building materials at the wrong place because the dumpsters have been moved.
The geographical coordinates of access roads, parking areas, and storage sites are recorded with unique geographical coordinates and updated as necessary.
Truck drivers know what to look out for thanks to visual, multilingual driver instructions that can be sent in advance.
Thanks to precise coordinates, the current location for loading or unloading the respective materials is always known.
The freight forwarder and its dispatcher know the requirements in advance and select the vehicle and technical equipment accordingly.
Changes to logistics on the construction site are directly accessible to everyone and can be tracked via the change history.
Loady use cases from logistics in the construction industry (extract)

Avoiding misunderstandings and making communication easy
Clear, standardized loading requirements reduce manual coordination, waiting times and frustrations — everyone knows how to get to a construction site right now and where and how to deliver or pick up the materials.

Communication with new and foreign-language drivers and foreign workers
Multilingualism of information and visually appealing instructions make it easier for drivers to communicate and get along on the construction site.

Online access options - without integration
Cooperation with many trades and changing service providers and drivers on a construction site is ensured by multilingual online views. Integrating and managing users is not necessary per se.
Mastering the challenge of “loading requirements” in chemical transport
Complex coordination of loading requirements between suppliers, customers, and freight forwarders.
Trucks are rejected or suffer delays at gates or loading points, loadings slots are lost.
Specific Instructions for temperature-controlled transport, for example, must be communicated individually.
Preparing customer unloading requirements for freight tenders takes months and is only possible with insufficient quality.
Pre-product restrictions are handled inconsistently and manually, resulting in errors and unnecessary costs due to rejected trucks or product contamination.
All parties involved in logistics have access to structured, up-to-date loading requirements.
Trucks can be planned and dispatched correctly, and there are 50% fewer truck rejections and incidents.
All data sets relating to transport requirements are available digitally and in multiple languages, and are passed on in full.
The structured data model and the increasingly collaborative use of loading requirements reduce the effort involved in freight tenders by 80%.
The central database for preload restrictions ensures greater transparency and product safety—and prevents downtime.
Loady use cases from logistics in the chemical industry (extract)

Cost savings through efficient logistics processes
The effort involved in data maintenance—especially for business partners—is steadily decreasing, while data quality is improving. This means fewer lost loading slots and fewer wasted trips, which saves demurrage charges and personnel costs and avoids unnecessary additional mileage.

Optimization and security through centralized preload restrictions
Managing preload restrictions in a logical structure makes it easy for carriers to query and select the right tank container, even with over 1,000 existing restrictions, and for chemical companies to perform automated checks at the gate.

Resilient logistics and easy communication
Loady's standardized and collaborative approach makes transport more reliable and predictable, even with changing carriers and drivers—whether for pickup, delivery, or self-pickup from the supplier.
Mastering the challenge of “loading requirements" in Distribution and Retail
Complex coordination between a large number of suppliers, suppliers and customers.
Many routes - especially with complex transport requirements - can only be traveled by special freight forwarders.
Tedious briefing from new drivers, whether about parking spaces or local processes.
Freight tenders are often not possible due to the large amount of data - and established freight forwarders seem to have no alternative, otherwise there is a risk of charges and incidents.
Unnecessary waiting times and delays lead to additional costs, such as waiting fees.
Customers' unloading data is increasingly maintained by themselves and requires less effort in data storage and communication.
Better data and understandable information reduce incidents and delays during transportation.
Structured data can be used digitally, e.g. in TMS/SAP S4/HANA, telematics.
More flexibility with regard to logistics partners — and with our own logistics companies with regard to changing drivers or dispatchers.
Digital processes and lower costs in transportation.
Loady use cases from distribution and retail logistics (extract)

Reduce costs through more efficient processes
Klare, standardisierte, mehrsprachige Ladeanforderungen reduzieren den individuellen Abstimmungsbedarf, Wartezeiten und Frustrationen.

Always up to date information
Changes to opening hours or closing days are synchronized so that shipments can be planned more reliably.

Better access and finding your way around on site
Accurate delivery addresses, geographic coordinates of parking spaces and relevant infrastructure, as well as visual driver instructions enable safe first and last miles.
Mastering the challenge of “loading requirements" in industrial manufacturing
Complex coordination between shippers, freight forwarders and drivers.
Trucks are parked at the gate or at the ramp and documents, technical or safety equipment are missing.
Drivers don't know where they have to go or how to behave on site.
Communication with drivers is often not possible due to language barriers.
Costs are increasing due to unnecessary waiting times and delays.
Shippers, freight forwarders and drivers use the same information and data.
Before a truck arrives at the production site, dispatchers and drivers know what they need to have with them.
The driver receives visual and easy-to-understand online instructions for their specific collection or delivery.
Data and instructions can be retrieved directly in several languages.
Costs are reduced as unnecessary journeys or delays due to lack of information are eliminated.
Loady use cases from logistics in the industrial production industry(extract)

Reduce costs through more efficient processes
Klare, standardisierte Ladeanforderungen reduzieren manuelle Abstimmungsbedarfe, Wartezeiten und Fehlfahrten - und somit Kosten.

Fewer waiting times and missed trips
Changes to opening hours, closing days or directions are synchronized in real time so that shipments take place without delays.

Simple, clear communication — across all channels
The information and data are shared with freight forwarders, who in turn can give their sub-contractors and drivers direct access.
Mastering the challenge of “loading requirements" in food and feed
Complex coordination between producer, logistician, freight forwarder, driver and warehouse — including delivery addresses and geographical coordinates.
There are many requirements in PDFs, emails or phone notes — this means manual searches and 1:1 reconciliations by phone or email.
Language barriers make communication with drivers increasingly difficult.
Compliance with strict requirements and hygiene regulations is difficult, especially when it comes to cleaning regulations and documents.
A lack of technical equipment — such as pumps or connectors — causes delays and empty runs.
Producer, logistician, freight forwarder, driver and warehouse access centrally stored information — including valid delivery addresses and geographical coordinates.
The data is stored in standardized formats and can be integrated directly into the various logistics processes.
Both data and driver instructions are directly available in several languages.
Companies in the food and feed industry set clear requirements for cleaning and permitted precursors, as well as documents to be presented.
Dispatchers plan trips and correctly equip trucks based on clear information.
Loady use cases from the logistics in the food and feed industry (extract)

Cost reduction through efficient logistics processes
Clear, standardized loading requirements reduce manual coordination requirements, waiting times, incorrect runs and costs.

The right choice of vehicle and equipment
Freight forwarders receive clear information on required technical equipment, permitted/prohibited subpoenas, documents.

Overcoming language barriers
Producers, dispatchers, drivers and warehouse operators manage and use the data in their language — this includes multilingual, visual driver instructions.
Mastering the challenge of “loading requirements" in mechanical engineering
Individual coordination between manufacturers, goods recipients, warehouse operators and logistics service providers is often required.
Relevant information is passed on from “data silos” via telephone, email or PDF; there are no standardized data sets.
Trucks load or unload incorrectly due to the wide range of variants and individuality of the products (dimensions, weights, instructions, etc.).
Special requirements for loading equipment, cranes, forklifts, safety materials, etc. are often not passed on or read correctly.
Logistics costs are increasing due to incorrect trips, unnecessary waiting times and delays, incidents and expenses in communication and troubleshooting.
Digital, unambiguous and direct coordination and access to current data for all parties involved in the specific transport.
The innovative, collaborative approach reduces data management costs and ensures reliable information.
Trucks have what they need and know the local conditions, requirements and facilities.
The right trailers and means of transport are used — there are fewer incidents and delays.
Valid data, which is used and shared directly in processes and systems, makes processes more efficient and reduces costs.
Loady use cases from the logistics in the mechanical engineering industry (extract)

Reduce costs through more efficient processes
Clear, standardized loading requirements reduce manual coordination, waiting times and incorrect runs — this saves costs and emissions.

Better planning without incidents
Changes to opening hours or security requirements are synchronized in real time so that shipments run without delays.

Standardised data model for loading requirements depending on the industry
Chemical parks with multiple service providers benefit from centrally managed loading requirements that are automatically synchronized and available to all parties involved.
Mastering the challenge of “loading requirements" in transport and logistics
Complex coordination with clients and sub-contractors/drivers.
Unstructured freight tenders with unclear information make the offer process more difficult.
A lack of clarity on delivery addresses, directions, parking, local processes, slot booking, PPA, equipment, pre-loading restrictions lead to truck refusals and delays.
It requires parallel, proprietary data collection on requirements to ensure the preparation of offers, planning, scheduling and execution of transports.
Manual efforts, inefficiencies, and delays lead to higher costs and reduce productivity and competitiveness.
Structured and up-to-date loading requirements are available and sub-contractors and drivers can access them directly.
Creating offers for freight tenders is 50% of the time with structured data, and even faster for subsequent customers.
Secure first and last miles and greater predictability — less coordination and frustration among drivers, transport managers and dispatchers.
The cost and transport-relevant information is available digitally and can be integrated with your own systems (TMS, match-making, telematics).
Lower costs, more competitiveness, better service quality and happier employees, drivers (!) , partners and customers.
Loady use cases from logistics service providers. (extract)

Valid requirements integrated directly into your own systems
End-to-end data sets from Loady support a match-making tool for answering freight tenders, planning tools or telematics directly in the TMS.

Geolocations enriched with information available directly via telematics
Validated geocoordinates with current, multilingual logistics requirements make it easier for drivers to get along on site and enable better planning.

Especially for bulk transport in chemicals: pre-loading restrictions
The central database with pre-loading restrictions from companies makes it easier to select and correctly clean the vehicle and helps to avoid truck refusals.
Loady enables shippers, logistics providers, and consignees to share a single source of truth.
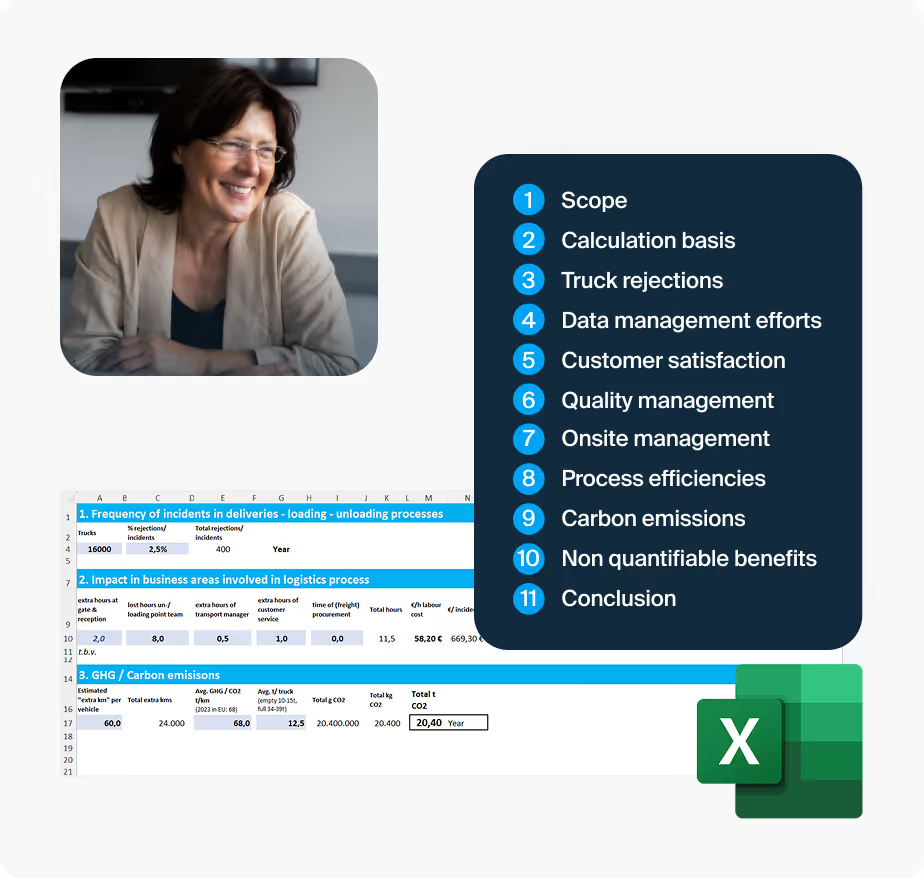
Benefit case — clear evidence of potential savings
If necessary, we will create a benefit case that shows the benefits and savings potential of Loady for your company — with real figures and a clear ROI assessment for a well-founded decision.
- Analysis of current transport processes & challenges
- Calculation of savings potential with the Loady Benefit calculator
- Interviews with key stakeholders for realistic scenarios
Outcome: A robust benefit case for decision-making